The Coming Tech-led Boom is a recent article published in the Wall Street Journal.
In January 2012, we sit again on the cusp of three grand technological transformations with the potential to rival that of the past century. All find their epicenters in America: big data, smart manufacturing and the wireless revolution.
Now, that’s what I call timing because I’ve been staking out the ground on two of those technological transformation – Smarter Manufacturing here on this blog and Big Data (at my new blog: Pachydata.com). Alas, as far as Smarter Manufacturing is concerned, I’m more concerned about effective manufacturing and elaborating on the fundamentals of manufacturing carried out in an intensely competitive environment.
The Smarter Manufacturing that the authors of the article had in mind is as follows:
While we see evidence already in automation and information systems applied to supply-chain management, we are just entering an era where the very fabrication of physical things is revolutionized by emerging materials science. Engineers will soon design and build from the molecular level, optimizing features and even creating new materials, radically improving quality and reducing waste.
Devices and products are already appearing based on computationally engineered materials that literally did not exist a few years ago: novel metal alloys, graphene instead of silicon transistors (graphene and carbon enable a radically new class of electronic and structural materials), and meta-materials that possess properties not possible in nature; e.g., rendering an object invisible—speculation about which received understandable recent publicity.
This era of new materials will be economically explosive when combined with 3-D printing, also known as direct-digital manufacturing—literally "printing" parts and devices using computational power, lasers and basic powdered metals and plastics. Already emerging are printed parts for high-value applications like patient-specific implants for hip joints or teeth, or lighter and stronger aircraft parts. Then one day, the Holy Grail: "desktop" printing of entire final products from wheels to even washing machines.
Such a radical shift is definitely possible but that changes the very idea of manufacturing as it has existed over the last three centuries. It’s not Smarter Manufacturing as much as it is desktop manufacturing.
Ok, so one out of three – not bad at all.
Two recent articles, one being the retelling of another, delve into some of the reasons why Apple makes iPhones in China and by implication not in the USA. The original article was from the New York Times, How the US lost out on iPhone Work and the retelling was recounted in This Article Explains why Apple makes iPhones in China and why the US is screwed.
There is no article about China which doesn’t recount some of the following snippets:
When one reads about these working conditions — 12-16 hour shifts, pay of ~$1 per hour or less, dormitories with 15 beds in 12×12 rooms
For Mr. Cook, the focus on Asia “came down to two things,” said one former high-ranking Apple executive. Factories in Asia “can scale up and down faster” and “Asian supply chains have surpassed what’s in the U.S.”
“The entire supply chain is in China now,” said another former high-ranking Apple executive. “You need a thousand rubber gaskets? That’s the factory next door. You need a million screws? That factory is a block away. You need that screw made a little bit different? It will take three hours.”
“The entire supply chain is in China now,” said another former high-ranking Apple executive. “You need a thousand rubber gaskets? That’s the factory next door. You need a million screws? That factory is a block away. You need that screw made a little bit different? It will take three hours.”
That’s because nothing like Foxconn City exists in the United States.
The facility has 230,000 employees, many working six days a week, often spending up to 12 hours a day at the plant. Over a quarter of Foxconn’s work force lives in company barracks and many workers earn less than $17 a day.
And lastly,
The answers, almost every time, were found outside the United States. Though components differ between versions, all iPhones contain hundreds of parts, an estimated 90 percent of which are manufactured abroad. Advanced semiconductors have come from Germany and Taiwan, memory from Korea and Japan, display panels and circuitry from Korea and Taiwan, chipsets from Europe and rare metals from Africa and Asia. And all of it is put together in China.
Summarizing, Chinese firms can scale up and down rapidly i.e. they have flexibility that the Chinese government and populace are willing to allow. Something that cannot be obtained stateside in whatever shape or form. The key takeaway is that it is not only scale but the willingness and ability to go either way with it. In the US, one finds that scale is directed one way towards growth but scaling down is an arduous, acrimonious and drawn out affair if it ever happens.
So here’s the first key to Smarter Manufacturing – Flexibility and Scalability.
In an earlier post, I blogged about the Baltic Dry Index as a good indicator of economic activity (Read it here: Ready for a recession?)
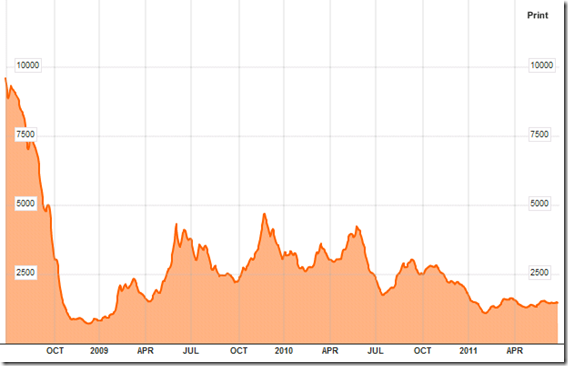
Even if we were to magically start moving in the Baltic Dry Index in a positive direction which would be a tremendous relief for everyone (but remember – *magically*), the US treasury and the Federal Reserve would continue to devalue the US dollar for two practical reasons:
1) Repay outstanding debts with a depreciated currency. This is really quid pro quo with some of the trading partners of the US against whom the US has been running trade deficits for the better part of a decade. The whole point of trade is not for one side of the equation to accumulate a lot of paper currency but to reciprocate in buying the origin country’s exports.
2) Make US exports competitive with other countries and reignite production/manufacturing stateside.
In fact, if the US (and World) economy were to recover some what, the above two agencies would devalue the US dollar with a vengeance.
This sort of policy, if successful, would mean a repatriation of some of the manufacturing that went overseas. Going further, when US firms look at the scenario (albeit a few years down the line) and see that the assets created overseas for manufacturing whatever widgets were outsourced have depreciated or is in need of upgrades to remain viable, that would be the decision point for deciding where the next generation of manufacturing will be located.
Much of the trajectory of what we see taking place goes to answering that question of the future and the above two agencies are hell bent on creating conditions that answer this question of manufacturing in the positive.
Or so I believe.
In such a scenario, what I believe to be key to long term competitive manufacturing is the ability to be smart about manufacturing – it means being able to operate using a very thin buffer for error because American firms will be competing with overseas firms (firm benefiting from their own countries’ competitive devaluation) that will continue to compete on large volumes and scale.
So what is Smarter Manufacturing?